The fiber quality requirements of fiberboard manufacturing are generally determined according to product category, production process and equipment status. As far as fiber quality is concerned, the separated fibers are required to have a certain specific surface area and good interweaving properties, and require a certain aspect ratio, sieve value, and fiber drainage, air permeability, chemical components, and fiber polymerization. There are strict requirements. Such as wet production, in the process of slab forming and hot pressing, the fiber slab is required to have the function of rapid and easy dehydration. The dry production requires not only ideal interweaving of the fibers, but also good air permeability of the slab. Otherwise, the formed slabs of the two production methods will destroy the structure of the slabs and affect the intrinsic quality of the products during transportation and hot pressing. However, when producing low-density or soft fiberboard, the fiber may not be pre-pressed or lightly pressed to dry it into a board after forming a slab. The degree of brooming increases the interweaving and contact area between the fibers themselves.
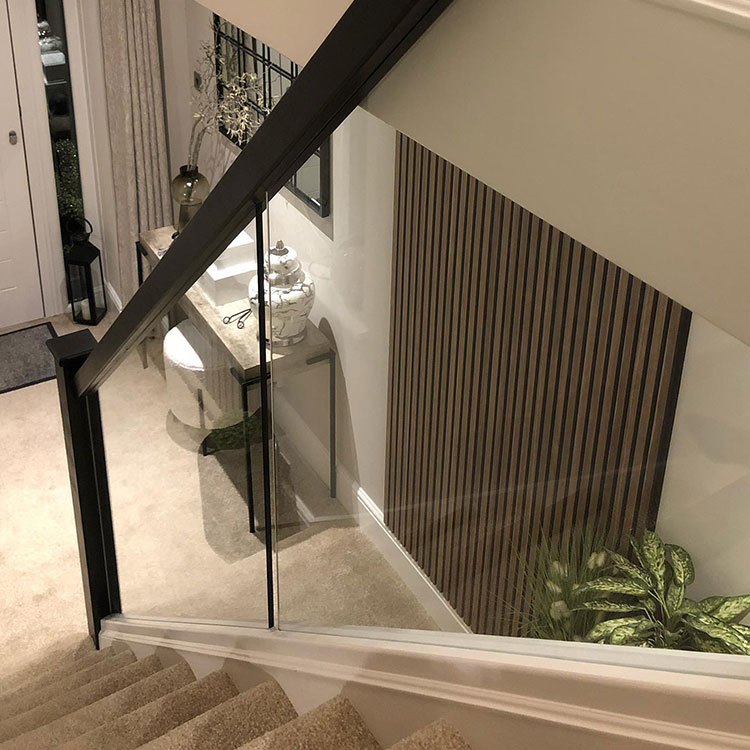
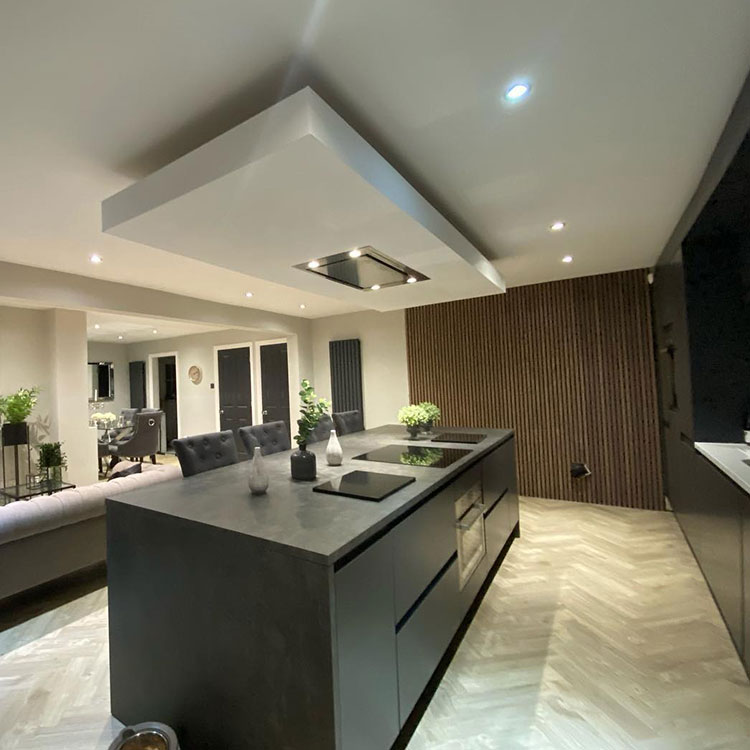
(1) The relationship between fiber morphology and product quality
As far as the inherent shape of the fiber is concerned, there are great differences between different raw materials. For example, the average length of fiber tracheids of coniferous wood is 2-3 mm, and the aspect ratio is 63-110; the average length of fiber tracheids and tough wood fibers of broad-leaved wood is 0.8-1.3 mm, and the aspect ratio is 35-110 58; as for grass fiber raw materials, the average length of fiber tracheids is only 0.8-2.2 mm, the aspect ratio is 30-130, and the content of non-fiber cells is relatively high.
From the perspective of fiber length and aspect ratio, it seems that the fiberboard made of softwood fibers is better. However, it has been proved that the performance of the fiberboard pressed by all coniferous materials is not necessarily the best. This is because the thickness of the fiber tracheids of coniferous materials is tubular, and the thickness of the cell wall is relatively larger than the width of the fibers. The total contact area becomes smaller. On the contrary, the fiber tracheids, tough wood fibers, and conduits of broad-leaved wood are thin-walled and band-shaped, so that the contact area between fibers is large, and the interweaving property is good. Fibreboard product with high density and strength.
The inherent strength of the fiber itself also has a certain influence on the strength of the fiberboard product. Someone once used the dyeing method to pass the bending and tensile failure tests of the hard fiberboard, and observed under the microscope, it was seen that 60% to 70% of the single fibers were damaged. From the conclusion of the test, it is believed that the inherent strength of the monomer fiber itself has almost no influence on the strength of the soft fiberboard with a density of 0.25-0.4g/cm3. It has a more obvious effect on the strength of medium density fiberboard with a density of 0.4-0.8g/cm3. It will have a greater impact on the strength of high-density fiberboards with a density greater than 0.9g/cm3. This is because the inherent strength of the single fiber itself is related to the average length of the cellulose chain (that is, the degree of polymerization), and the breaking length of a single fiber can reach 40000Pm. After the fibers are paved and formed into slabs, the irregular arrangement is in a state of being scattered and irregular. After eliminating the influence of other factors, assuming that the average breaking length of the single fiber is 20 000 Pm, and then calculated according to a conservative number of 40%, the single fiber The fracture length can reach 8 000 Pm. It can be seen that the relationship between the inherent strength of the fiber itself and the strength of the fiberboard product.
(2) The relationship between the degree of fiber separation and the quality of fiberboard
The degree of fiber separation refers to the degree of fiber separation after defibration, which is an aspect that indirectly reflects the quality of fibers. The finer the fiber separation, the larger the specific surface area of the fiber, and the poorer the water drainage and air permeability of the fiber. Conversely, the better the water filtration and air permeability of the fiber, but the fiber at this time is often thicker and the specific surface area of the fiber is correspondingly smaller. After fiber separation, the specific surface area of the fiber is inversely proportional to the water drainage. The larger the specific surface area is, the more fine fibers are, and the worse the water drainage of the fiber is. Poor fiber separation degree Coarse fiber (28~48 mesh) has small air resistance, while high fiber separation degree and fine fiber have large specific surface area (100~200 mesh), poor air permeability of fiber, good slab filling, but large air resistance. The larger the specific surface area of the fiber, the smaller the volume of the fiber, and vice versa. Thus it can be deduced that the filterability, air permeability and volume of the fiber all have a certain relationship with the degree of separation of the fiber. Therefore, it can be said that the degree of fiber separation is an important indicator of the quality of fiber pulp, which directly affects the fiber production process and product quality. Practice has also proved that within a certain range, the higher the degree of fiber separation, that is, the finer the fibers, the better the interweaving between the fibers of the slab, and the strength, water resistance and product density of the fiberboard will also increase accordingly.
In addition, it is concluded from practical experience that the degree of fiber separation should be controlled within a certain range on the basis of stabilizing product quality according to different types of products and process characteristics.
(3) Relationship between fiber screening value and fiberboard quality
The fiber shape, fiber length, and fiber thickness ratio of different types of fiber raw materials will have varying degrees of impact on the quality of fiberboard. The method of testing fiber quality is usually to use fiber separation (fiber freeness DS and fiber percussion degree SR). Because the fiber itself is very different, it is often difficult to reflect the essence of fiber quality by measuring the degree of separation of fibers alone. Sometimes the freeness values of the two fibers are basically similar, but the length and thickness ratio of the fibers are different. Therefore, it is supplemented by testing the fiber sieving value to analyze the quality of the separated fiber.
The fiber screening value is of great significance in actual production. Adjusting the fiber slurry screening value can improve the fiber shape and slurry properties, thereby improving the quality of fiberboard products. The research on the effect of fiber screening value on the quality of fiberboard has long been paid attention to, and regular technical basis has been obtained. The fiber morphology is mainly affected by the material type and the method of fiber separation. The coniferous wood is better than the broad-leaved wood fiber. The chemical mechanical method is better than the heating mechanical method (that is, the thermal grinding method), and the pure mechanical method is more effective. poor.
Dongguan MUMU Woodworking Co., Ltd. is a Chinese sound-absorbing building material manufacturer and supplier. Please contact us for more information!
Post time: Jul-22-2023