Mit der rasanten Entwicklung der Wirtschaft meines Landes und der Verbesserung des Lebensstandards der Stadt- und Landbewohner ist es zu einer beliebten Konsummode geworden, umfassende Innendekorationen und Möbelerneuerungen durchzuführen.Allerdings werden Holzwerkstoffplatten häufig als Grundmaterialien in der Innendekorations- und Möbelindustrie verwendet, sodass ein Problem der Formaldehydbelastung besteht.In der Vergangenheit war das wirtschaftliche Einkommen der Menschen gering, die meisten Innendekorationen wurden nur teilweise durchgeführt und die Möbel wurden oft in geringem Umfang modernisiert, sodass die Formaldehydverschmutzung nicht sehr ausgeprägt war und toleriert werden konnte.
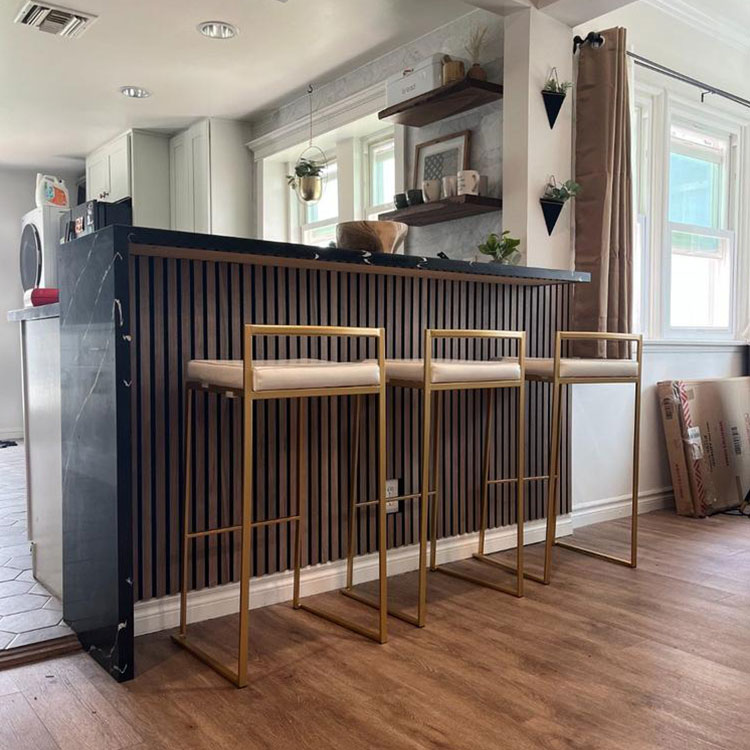
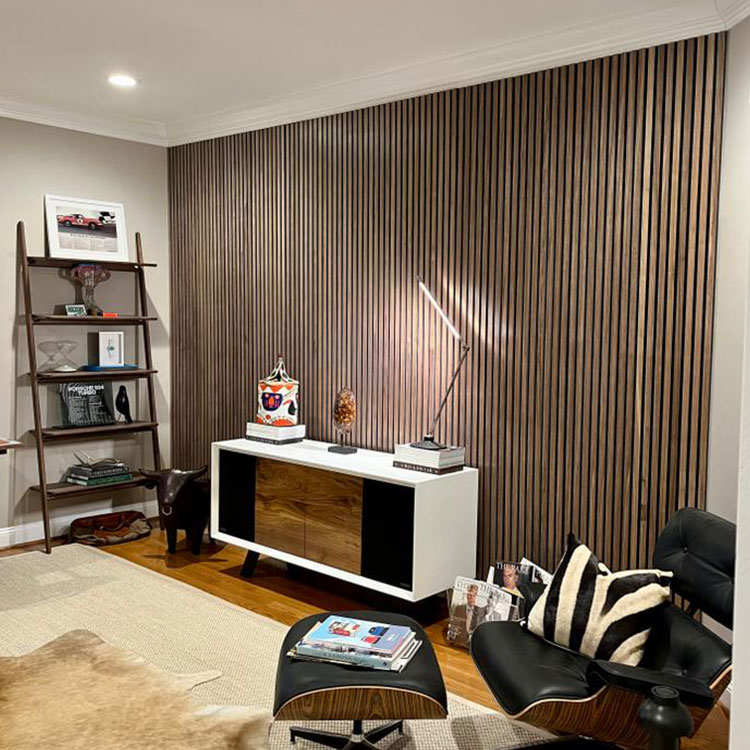
Heutzutage ist es fast schon üblich, dass jeder, der in ein neues Zuhause zieht, umfangreiche Renovierungen und Möbelerneuerungen durchführt.Auf diese Weise nimmt die Anreicherung der Formaldehydverflüchtigung stark zu, erreicht ein unerträgliches Maß und gefährdet unmittelbar den Wohnraum der Nutzer.Aus diesem Grund ist der Streit zwischen der Dekorationsabteilung und dem Nutzer zu einem gesellschaftlichen Problem geworden, und die Rohstoffe für Dekoration oder Möbel kommen vom Markt, und es gibt keine Möglichkeit, ihn zu lösen.Mit der Verbesserung des Umweltschutzbewusstseins auf der ganzen Welt hat die durch Formaldehydgas verursachte Verschmutzung ein Ausmaß erreicht, dem Aufmerksamkeit geschenkt werden muss.Aus diesem Grund haben Wissenschaftler und Techniker viele Maßnahmen erarbeitet und versuchen, diese zu lösen.Zum Beispiel die Verbesserung der vernünftigen Formel von Harnstoff und Formaldehyd oder sogar die Verwendung von Formaldehydfängern usw., aber sie sind keine radikale Lösung.Darüber hinaus erlauben die Verpackungsmaterialien bestimmter Waren wie Lebensmittel, Tee, Zigaretten usw. kein Vorhandensein von Formaldehyd.Früher wurde überwiegend Naturholz verwendet.Aufgrund der Umsetzung der nationalen Politik zum Schutz der Waldressourcen wurde die Verwendung von Holzverpackungsmaterialien eingeschränkt.Bei der Suche nach alternativen Materialien sind Holzwerkstoffplatten die erste Wahl.Aufgrund der Belastung durch Formaldehyd ist dies jedoch schwierig zu realisieren.All dies macht die Forderung nach schadstofffreien „grünen Holzwerkstoffen“ auf der Tagesordnung.Die Quelle der Freisetzung von Formaldehydgas ist der bei der Herstellung von Holzwerkstoffplatten verwendete Klebstoff – Harnstoff-Formaldehydharz.Der größte Vorteil dieser Art von Klebstoff besteht darin, dass die Rohstoffquelle reichlich vorhanden ist, die Leistung gut ist, der Preis niedrig ist und es derzeit keinen Ersatz gibt.Harnstoff-Formaldehyd-Harz ist jedoch durch den Syntheseprozess begrenzt.Unabhängig davon, wie die Formel verbessert wird, kann die chemische Reaktion nicht perfekt sein.Bei der Herstellung und Verwendung des Produkts besteht immer das Problem, dass überschüssiges Formaldehyd freigesetzt und reagiert, und zwar nur in der Menge.Wenn der Syntheseprozess rückwärts verläuft, wird mehr Formaldehydgas freigesetzt.Unter den vielen Holzwerkstoffunternehmen in unserem Land ist die Synthesetechnologie von Harnstoff-Formaldehyd-Harz sehr veraltet, so dass es nicht verwunderlich ist, dass die auf den Markt kommenden Holzwerkstoffe eine erhebliche Umweltverschmutzung verursachen.Es gibt keine formaldehydfreien Leimtypen, aber entweder ist die Leimquelle knapp oder der Preis ist hoch.Nach der aktuellen Produktion von Holzwerkstoffen in meinem Land beträgt der jährliche Flüssigklebstoffverbrauch etwa 3 Millionen Tonnen, was schwer zu decken ist.Und das billigste Kunstharz der heutigen Zeit ist nur Harnstoffleim.
Es ist schwierig, den Widerspruch zwischen Schadstoffreduzierung, Kosten und Leimquelle in naher Zukunft in Einklang zu bringen.Daher erforschen Wissenschaftler im In- und Ausland einen anderen Weg, nämlich die Herstellung von Holzwerkstoffplatten mit einem leimfreien Verfahren.Vor mehr als 30 Jahren haben die Sowjetunion und die Tschechische Republik die Machbarkeitsstudie zu Theorie und Technologie abgeschlossen, und die Tschechische Republik führte auch eine Produktion in kleinem Maßstab durch.Ich weiß nicht, warum ich es nicht weiter studiert habe?Vielleicht liegt der Hauptgrund darin, dass das Ausmaß der Umweltverschmutzung damals nicht die Aufmerksamkeit der Gesellschaft auf sich zog und die treibende Kraft der Nachfrage verloren ging, sodass sie nicht bereit war, den Produktionsprozess weiter zu verbessern.
Mittlerweile hat das Bewusstsein für den Umweltschutz ein beispielloses Ausmaß erreicht und gleichzeitig können es die Nutzer in der Praxis kaum ertragen.Andernfalls würde Japan keinen Formaldehydfänger produzieren.Daher haben Wissenschaftler im In- und Ausland der Erforschung dieses Themas mehr Aufmerksamkeit geschenkt, verschiedene technische Wege eingeschlagen und jeweils bestimmte Ergebnisse erzielt.Allerdings hat keiner von ihnen eine groß angelegte Produktion aufgebaut, um die Produkte auf den Markt zu bringen.Die Entwicklung leimfreier Holzwerkstoffplatten ist der effektivste Weg zur Lösung von Umweltverschmutzung und gleichzeitig ein Entwicklungstrend.Gegenwärtig herrscht ein Wettbewerb zwischen technologischer Innovation und Zeit. Wer über die fortschrittlichste, einfachste und am einfachsten zu fördernde Technologie verfügt, wird als erster die Produktivität steigern und den Markt besetzen.
Nach der Klebetheorie, dass Pflanzenfasern selbstklebend sein können, was von den Vorgängern durch wiederholte Tests und kontinuierliche Optimierung bestätigt wurde, wurde ein Durchbruch im Prozess der Bildung von nicht klebenden Faserplatten erzielt.Der Schlüssel, den es zu überwinden gilt, besteht darin, die Leistung der nicht verleimten Platten zu verbessern und die Betriebsabläufe zu vereinfachen. Die vorhandene Produktionslinie für mitteldichte Faserplatten kann zur Herstellung von leimfreien Faserplatten genutzt werden, ohne dass Änderungen an der gesamten Produktionsausrüstung (nur der Leimherstellungsausrüstung) vorgenommen werden müssen außer Betrieb ist).Die mechanische Festigkeit des Produkts entspricht der von gewöhnlichen Spanplatten oder ist höher als diese, und die Wasserdichtigkeit ist dieselbe wie die von Harnstofffaserplatten.
Da Wasser als „Klebstoff“ verwendet wird, wird die Selbstklebekraft zwischen den Fasern während des Heißpressvorgangs vervollständigt, sodass der Feuchtigkeitsgehalt der Platte höher ist als der der Schlichteplatte und der Heißpresszyklus verlängert werden muss um sicherzustellen, dass die chemische Reaktion vollständig abgeschlossen ist, was sich auf die ursprüngliche Produktivität auswirkt, jedoch keinen Einfluss auf die tatsächliche Wirtschaftsleistung hat.
1. Die Einsparung von Klebstoffkosten ist ein direkter Vorteil und erhöht den Nettogewinn.
2. Das Produkt hat keine verfestigte Schicht, weniger Schleifen, weniger Stromverbrauch sowie geringeren Stromverbrauch und geringere Schleifbandkosten.
3. Der größte Teil des Wassers in der Bramme wird zur Verdampfung in die Presse übertragen, sodass ein Teil der konvektiven Wärmeübertragung im Trockner in Kontaktwärmeübertragung umgewandelt wird, der thermische Wirkungsgrad verbessert und der Kohleverbrauch reduziert wird.Dies sind zusätzliche Vorteile.
Allein für diese drei Artikel kann selbst bei einer Reduzierung der Jahresproduktion von 30.000 m3 auf 15.000 bis 20.000 m3 immer noch ein Gewinn von 3,3 bis 4,4 Millionen Yuan pro Jahr erzielt werden (abhängig von den Leimkosten).Darüber hinaus werden nach der Reduzierung der Produktion auch der Rohstoff- und Energieverbrauch um 30 bis 50 % reduziert, Geräteverluste und Wartungskosten reduziert und das gesamte Betriebskapital reduziert.Dies ist der indirekte Nutzen, der generiert wird.Daher ist der Gesamtgewinn nicht niedriger oder sogar höher als der ursprüngliche Output.Es ist auch sehr einfach, die ursprüngliche Leistung beizubehalten, da sich die Produktionskapazität jeder Prozessausrüstung vor der Heißpresse nicht geändert hat. Dies kann also durch Hinzufügen einer Heißpresse und ihres Transportmechanismus oder durch Ändern der Anzahl der Schichten erreicht werden heisse Presse .Diese Renovierungsgebühr ist notwendig.
Der größte Vorteil leimloser Faserplatten ist die vollständige Eliminierung von Schadstoffquellen und die geringen Kosten, und ihre Verwendung kann auch auf Verpackungsmaterialien für bestimmte Waren ausgeweitet werden, die keine Umweltverschmutzung zulassen.Der natürliche Nachteil leimloser Faserplatten: Sie werden durch Selbstklebekraft verklebt, die durch die chemische Wirkung von Wasser und Fasermolekülen entsteht.Die Fasern müssen in engem Kontakt stehen, da sonst die Haftung verringert wird, sodass die Dichte höher ist als bei MDF mit normaler Größe.Dieser Fehler fällt bei der Herstellung dünner Bleche nicht auf.
DongguanMUMU Woodworking Co., Ltd.ist ein chinesischer Hersteller und Lieferant von schallabsorbierenden Baumaterialien.Bittekontaktiere unsfür mehr Informationen!
Zeitpunkt der Veröffentlichung: 31. Juli 2023