With the rapid development of my country's economy and the improvement of the living standards of urban and rural residents, it has become a popular consumption fashion to carry out comprehensive interior decoration and furniture renewal. However, wood-based panels are widely used as base materials in interior decoration and furniture industries, so there is a problem of formaldehyde pollution. In the past, people's economic income was low, most of the interior decoration was only partially carried out, and the furniture was often updated in a small amount, so the formaldehyde pollution was not very prominent and could be tolerated.
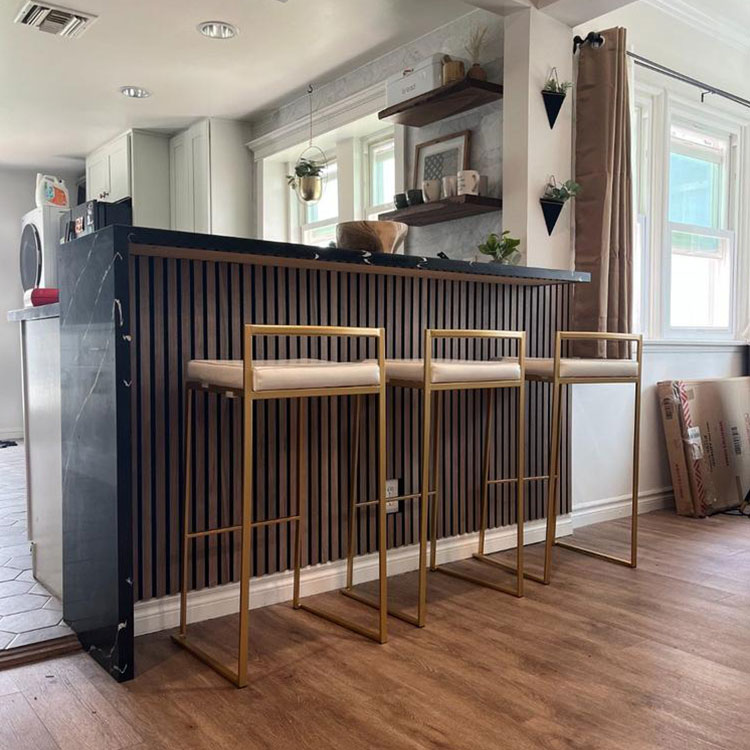
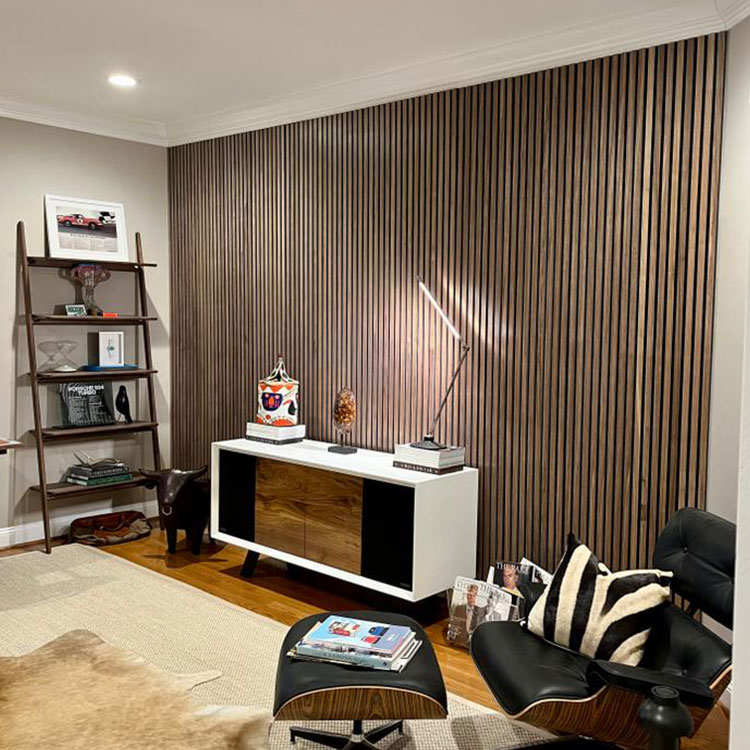
Nowadays, it is almost common for those who move into a new home to carry out comprehensive renovations and furniture updates. In this way, the accumulation of formaldehyde volatilization increases greatly, reaching an unbearable level, directly endangering the living space of users. For this reason, the dispute between the decoration department and the user has become a social problem, and the raw materials for decoration or furniture come from the market, and there is no way to solve it. With the improvement of environmental protection awareness all over the world, the pollution caused by formaldehyde gas has reached a level that must be paid attention to. For this reason, scientific and technological worker has worked out many measures and tries to solve. Such as improving the reasonable formula of urea and formaldehyde, or even using formaldehyde scavengers, etc., but they are not a radical solution. In addition, the packaging materials of certain commodities, such as food, tea, cigarettes, etc., do not allow the presence of formaldehyde. In the past, natural wood was mostly used. Due to the implementation of the national policy of protecting forest resources, the use of wood packaging materials has been restricted. When looking for alternative materials, wood-based panels are the first choice. However, it is difficult to realize due to the pollution of formaldehyde. All this makes the demand for pollution-free "green wood-based panels" on the agenda. The source of the release of formaldehyde gas is the adhesive used in the production of wood-based panels - urea-formaldehyde resin. The biggest advantage of this kind of adhesive is that the source of raw material is abundant, the performance is good, the price is low, and there is no substitute at present. However, urea-formaldehyde resin is limited by the synthesis process. No matter how the formula is improved, the chemical reaction cannot be perfect. During the manufacture and use of the product, there is always the problem of excess formaldehyde released and reacted, only the amount. If the synthesis process is backward, more formaldehyde gas will be released. Among the many wood-based panel enterprises in our country, the synthetic technology of urea-formaldehyde resin is very outdated, so it is not surprising that the wood-based panels entering the market cause serious pollution. There are no formaldehyde-free glue types, but either the glue source is scarce or the price is expensive. According to the current production of wood-based panels in my country, the annual liquid adhesive consumption is about 3 million tons, which is difficult to meet. And the cheapest synthetic resin in contemporary times is only urea glue.
It is difficult to reconcile the contradiction between pollution reduction, cost and glue source in the near future. Therefore, scholars at home and abroad are exploring another way, that is, to produce wood-based panels with a glue-free process. More than 30 years ago, the Soviet Union and the Czech Republic completed the feasibility study of theory and technology, and the Czech Republic also carried out small-scale production. I don't know why I didn't continue to study it? Perhaps the main reason is that the seriousness of pollution did not attract the attention of the society at that time, and the driving force of demand was lost, so it was unwilling to further improve the production process.
Now the awareness of environmental protection has reached an unprecedented height, and at the same time, in practice, users really can't bear it. Otherwise, Japan would not produce formaldehyde scavenger. Therefore, scholars at home and abroad have paid more attention to the research of this topic, adopted various technical routes, and achieved certain results respectively. However, none of them has formed large-scale productivity to make the products enter the market. The development of glue-free wood-based panels is the most effective way to solve environmental pollution, and it is also a development trend. At present, there is a competition between technological innovation and time, whoever has the most advanced, simplest and easiest-to-promote technology will be the first to form productivity and occupy the market.
According to the gluing theory that plant fibers can be self-adhesive, which has been confirmed by the predecessors, through repeated tests and continuous optimization, a breakthrough has been made in the process of forming non-glue fiberboard. The key to overcome is to improve the performance of the non-glue board and simplify the operating procedures It can make use of the existing medium density fiberboard production line to produce glueless fiberboard without making any changes to all production equipment (only the glue making equipment is out of use). The mechanical strength of the product is equivalent to or higher than that of ordinary particleboard, and the waterproof performance is the same as that of urea fiberboard.
Since water is used as the "adhesive", the self-adhesive force between the fibers is completed during the hot pressing process, so the moisture content of the slab is higher than that of the sizing slab, and the hot pressing cycle must be extended to ensure that the chemical reaction is fully completed, thereby affecting the original productivity, but has no effect on actual economic performance.
1. Saving adhesive costs is a direct benefit and increases net profit.
2. The product has no solidified layer, less sanding, less power consumption, and lower power consumption and abrasive belt costs.
3. Most of the water in the slab is transferred to the press to evaporate, so that part of the convective heat transfer in the dryer is converted into contact heat transfer, the thermal efficiency is improved, and the coal consumption is reduced. These are added benefits.
For these three items alone, even if the annual output is reduced from 30,000 m3 to 15,000 to 20,000 m3, it can still create a profit of 3.3 million to 4.4 million yuan per year (depending on the cost of glue). What's more, after the output is reduced, raw materials and energy consumption are also reduced by 30% to 50%, equipment loss and maintenance costs are also reduced, and the total working capital occupied is also reduced. This is the indirect benefit generated. Therefore, the total profit is not lower than the original output, or even higher. It is also very simple to maintain the original output, because the production capacity of each process equipment before the hot press has not changed, so it can be done by adding a hot press and its transport mechanism, or changing the number of layers of the hot press . This renovation fee is necessary.
The biggest advantage of glueless fiberboard is the complete elimination of pollution sources and low cost, and its use can also be extended to packaging materials for certain commodities that do not allow pollution. The natural defect of glueless fiberboard: it is glued by self-adhesive force generated by the chemical action of water and fiber molecules. The fibers must be in close contact, otherwise the adhesion will be reduced, so the density is higher than that of ordinary sized MDF. This defect is not noticeable if thin sheets are produced.
Dongguan MUMU Woodworking Co., Ltd. is a Chinese sound-absorbing building material manufacturer and supplier. Please contact us for more information!
Post time: Jul-31-2023